Snelstaal (HSS): Eigenschappen en toepassingen
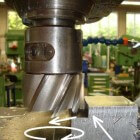

Algemene beschouwing
Snel(draai)staal ofwel High Speed Steel (HSS) is een hooggelegeerd gereedschapstaal dat tot circa 600 °C zijn hardheid en scherpte van de snijkanten behoudt, bestand is tegen stoten en na zachtgloeien gemakkelijker te bewerken. Het gebruik van snelstaal voor verspaning is voorbij gestreefd door hardmetaal, maar snelstaal wordt door genoemde voordelen naast snijgereedschap als boren en frezen voor een grote verscheidenheid aan gereedschap gebruikt, zoals stempels en matrijzen.Het herkennen van snelstalen snijgereedschap
De bases samenstelling van snelstaal is: Wolfraam 18%, Chroom 4% vanadium 1%, Koolstof 1%,de rest is ijzer. Men spreekt van 18-4-1 snelstaal (18%W- 4%Cr-1% V). Rond deze klassieke samenstelling zijn tientallen legeringen ontstaan, ontworpen voor even zovele specifieke toepassingen. Vaak worden goedkopere niet snelstalen boren e.d aan de klussers verkocht als echte snelstaal. Het verschil tussen snelstaal en gewoon laaggelegeerd gereedschapstaal is door de vonkenregen bij het slijpen van de boren gemakkelijk aan te tonen. Het snelstaal geeft donkere vonken en gewoon staal een veel lichtere vonkenregen.Invloed legeringselementen in snelstaal
- Wolfraam W vormt wolfraamcarbide, verhoogt de hardheid en warmhardheid en daarmee de slijtweerstand.
- Molybdeen Mo kan wolfraam aanvullen of vervangen voor de vorming van de harde molybdeencarbide. Het verbetert de taaiheid en even als wolfraam de warmhardheid en daarmee de slijtvastheid bij hogere werktemperaturen.
- Vanadium V vormt vanadiumcarbide die de slijtvastheid verhoogt en is met een hardheid van 9-9.5 Mohs het hardste materiaal op diamant na.
- Kobalt Co maakt deel uit van de matrix, het basismateriaal waarin de carbides ingebed zijn.
- Chroom Cr verbetert de carbide vorming en doorharding van het staal waardoor gereedschap met grotere doorsneden gehard kan worden. Chroomcarbide beperkt de korrelgroei hetgeen resulteert in een taai fijnkorrelig staal.
- Koolstof C vormt de harde martensiet structuur en is uiteraard nodig voor de carbide vorming. Het koolstofgehalte wordt aangepast aan het gehalte van de elementen waarmee het de carbides moet vormen.
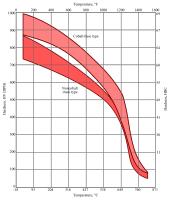
Warmtebehandeling van snelstaal
ZachtgloeienZachtgloeien om de bewerkbaarheid van het snelstaal te verbeteren. Verwarmen op 800-900 °C en langzaam afkoelen in de oven. Resultaat is een Brinell hardheid 250-300 HB. Na bewerken van het staal door verspanen of kouddeformatie moeten de bewerking spanningen gereduceerd worden door spanningsarmgloeien, dat betekent circa 1 uur verwarmen op circa 600 °C, gevolgd door afkoelen in lucht. Het product kan nu gehard worden.
Secundair harden ofwel precipitatie harden
Het staal wordt gelegeerd met W, Cr, V, Mo en Co, het staal wordt hoog in het austeniet gebied verhit waardoor de meeste elementen oplossen in het austeniet. Het austeniet wordt afgeschrikt vanaf 1200 - 1300 en "ontlaten" bij circa 600°C voor het z.g.n. secundair harden. Het secundair harden is de bases van snelstaal.
Harden door precipitatie
Vooraf aan het (secundair) harden wordt het staal oplossend gegloeid om de aanwezige uitscheidingen (precipitaten) in het austeniet op te lossen. Nadat het staal deze behandeling heeft ondergaan heeft het een homogene mengkristal structuur. In veel gevallen wordt gesproken van zachtgloeien wat hetzelfde resultaat oplevert. Zachtgegloeid snelstaal (hardheid ca250- 300HB) is goed te bewerken.
Precipitatieharden treedt op omdat de oplosbaarheid van de in het austeniet opgeloste legeringsbestanddelen (v.n.l koolstof) bij dalende temperatuur terugloopt door krimpen van het rooster. De opgeloste stoffen staan onder hoge uitscheidingsdruk. Deze druk wordt zeer groot bij het omklappen van austeniet (KVR) rooster in het ferriet (KRR) rooster dat geen ruimte heeft voor de opgeloste elementen. Het uitscheiden kost tijd en bij snel afkoelen (afschrikken) worden deze opgeloste stoffen ingevroren.Door de interne spanning ontstaat een vervormd KRR-rooster. Het wordt door de ingesloten legeringsbestanddelen opgerekt tot een tatragonaal rooster die een ongeveer 2% grotere ruimte inneemt. Austeniet dat nog niet is omgezet komt onder een toenemde druk te staan door de uitzetting van het omringende (tetragonale) martensiet en kan daardoor niet transformeren tot martensiet. We noemen het restausteniet, de transformatie van het restausteniet tot martensiet wordt dus onderdrukt. De transformatie temperatuur nodig voor de omzetting van austenitische KVR rooster in het tetragonale martensiet moet beneden nul graden afkoelen, het z.g.n. diepkoelen, in vloeibaar gas tussen -70 en -196°C, afhankelijk van de legering, om het laatste restausteniet om te zetten in martensiet.
Samenvatting van het precipitatieharden
- Oplossend gloeien hoog in het austeniet gebied om carbiden in het austeniet op te lossen. Verwarmingsstop op 850°C en op 1050°C om thermische spanningen veroorzaakt door temperatuur verschillen in het product, af te voeren.
- Afschrikken in olie of zoutbad van circa 550-600°C en daarin houden ("ontlaten") voor de diffusie van de carbiden uit de matrix tot eilandjes, het eigenlijke precipitatieharden
- Langzaam afkoelen in lucht. De hardheid is dan circa 65 HRC, in de praktijk de hoogst haalbare hardheid omdat verder opvoeren van de hardheid tot te grote brosheid leidt
Hardingsstructuur van snelstaal
In de microstructuur van sneldraaistaal zien we in de zachtgegloeide toestand bolvormige carbiden van het type molybdeen- of wolframcarbide en vanadiumcarbide in een matrix van ferriet. Als het staal na het harden wordt ontlaten op circa 550°C toont het fijn verdeelde carbiden in een matrix van martensiet die verantwoordelijk zijn voor de hardheid en slijtvastheid van het snelstaal.
Thermische scheuren
Ingewikkelde snelstalen gereedschapvormen mogen niet te snel verhit en afgekoeld worden wegens het gevaar van thermische spanningen door temperatuurverschillen. Keuze van de staalsoort wordt niet alleen bepaald door de gewenste mechanische eigenschappen maar ook door de ingewikkeldheid van het product die de maximale afkoelsnelheid bepaalt. Ingewikkeld gereedschap kan niet in water afgeschrikt worden wegens massaverschillen waardoor de temperatuur in het product niet overal dezelfde is tijdens verhitten en afkoelen en er inwendige spanningen ontstaan, die leiden tot vervorming en hardingsscheuren. Bij afkoeling van hoogwaardig staal kan men kiezen uit afkoelen in olie, in lucht of in de oven. Thermische spanningen kunnen veel later, tijdens gebruik, via moeilijk te vinden haarscheurtjes leiden tot fatale vermoeidheidsbreuk.Isotherm harden
Isotherm harden is getrapt harden. De legering wordt zolang verhit hoog in het austeniet gebied dat de carbide vormende elementen zijn opgelost. In tegenstelling tot het klassieke harden wordt het staal niet afgeschrikt tot kamertemperatuur maar in een warme zout- of oliebad boven de MS (Martensiet Start) temperatuur (circa 550 °C) en daar gehouden tot de carbiden zich door diffusie uitscheiden, daarna pas wordt het staal afgekoeld tot kamertemperatuur.
Snelstaal voor koudomvormgereedschap
Omdat de kennis van de metaalkundigen toeneemt wat het koudvervormen (koudomvormen) betreft komen er meer toepassingen voor snelstaal bij. Koudomvormen kan onderverdeeld worden in processen, zoals slagextrusie, dieptrekken, optrompen e.d. Voor elk specifiek proces zijn de eisen die aan het gereedschap gesteld worden anders. In de praktijk hebben de snelstalen zich bewezen als het geschikte staal voor omvormgereedschappen. Veel gebruikt voor het koud omvormen is snelstaal 1.3343.Tabel: Een selectie van toegepaste snelstalen en hun samenstelling. Fosfor en zwavel zijn elk max. 0,03%
Legering- EN/DIN | C | Si max | Mn max | Cr | Mo | V | W | Co |
---|---|---|---|---|---|---|---|---|
1.3351- HS6-5-4 | 1,35 | 0,45 | 0,4 | 4,1 | 5,0 | 4,1 | 5,9 | --- |
1.3247- HS6-9-1 | 1,1 | 0,45 | 0,4 | 3,9 | 9,2 | 1,0 | 1,4 | 7,8 |
1.3325 HS)-4-1 | 0,83 | 0,65 | 0,4 | 4,1 | 4,3 | 1,1 | --- | ----- |
1.3343 HS6-5-2C | 0,90 | 0,45 | 0,5 | 4,1 | 5,0 | 1,8 | 6,2 | --- |
1.3345 HS6-5-3C | 1,29 | 0,7 | 0,4 | 4,2 | 5,0 | 3,0 | 6,3 | --- |
1.3348 HS2-9-2 | 1,02 | 0,7 | 0,4 | 3,8 | 8,6 | 1,9 | 1,8 | --- |
1.3355 - HS18-0-1 | 0,76 | 0,45 | 0,45 | 4,0 | --- | 1,1 | 18 | --- |
1.3346 HS2-9-1 | 0,83 | 0,45 | 0,4 | 3,8 | 8,6 | 1,2 | 1,8 | --- |
1.3243 HS6-5-2-5 | 0,92 | 0,45 | 0,4 | 4,1 | 5,0 | 1,9 | 6,2 | 4,8 |
1,3344 HS6-5-3 | 1,21 | 0,45 | 0,4 | 4,1 | 5,0 | 2,9 | 6,2 | --- |
1.3244 HS6-5-3-8 | 1,29 | 0,7 | 0,4 | 4,2 | 5,0 | 3,0 | 6,3 | 8,4 |
1.3326 HS1-4-2 | 0,89 | 0,65 | 0,4 | 4,1 | 4,5 | [/TD][TD]1,9 | 1,2 | |
1.3207 HS10-4-3-1 | 1,26 | 0,45 | 0,4 | 4,1 | 3,5 | 3,25 | 9,3 | 10,0 |
Tabel: De fabrikant van het snelstaal levert een handleiding mee voor de warmtebehandeling. Zoals we zien bij de snelstalen in onderstaande tabel is de standaard hardingsprocedure voor alle legeringen praktisch gelijk. De hardheid na het harden en ontlaten ligt tussen 59 en 68 HRC en de zachtgloei hardheid (meestal in deze toestand door de fabriek geleverd) ligt tussen 250 en 300 HB. Afhankelijk van het product (wanddikte verschillen en asymmetrie) en de klant eisen (taaier of harder) zijn talrijke variaties in de hardingsprocedure mogelijk. De procestemperaturen zijn belangrijk in verband met vervormen en (haar)scheuren. Zowel het verhitten als het afkoelen kan getrapt gebeuren om de warmte spanningen te reduceren die tijdens de warmtebehandeling ontstaan. Er is altijd overleg met de fabrikant en de harderij nodig om tot een kwaliteitsproduct te komen. De cijfers in de tabellen zijn richtwaarden, de definitieve gegevens behoren van de staalfabrikant en de harderij te komen.
legering-EN/DIN | zachtgl-temp °C | zachtgl-duur- uren | zachtgl-afkoel in: | harden- temp °C | harden- afkoel in: | ontlaat - temp °C | ontlaat - duur- uren | ontlaat- afkoel in: | trekst.-hardh. | gebruiks- hardheid -HRC |
---|---|---|---|---|---|---|---|---|---|---|
1.3355-HS18-0-1 | 850 | 2-5 | oven | 1270 | lucht | 550 | 3x1h | lucht | hardheid 270HB | 65 |
1.3346-HS2-9-1 | 835 | 2-5 | oven | 1195 | lucht | 545 | 2cycli van min. 2h | lucht | fabriek 265HB | 63 |
1.3243-HS6-5-2-5 | 810 | 2-5 | oven | 1215 | lucht | 565 | min 2h | lucht | 880 | 65 |
1.3344-HS6-5-3 | 800 | 2-5 | oven | 1220 | lucht | 550 | min2h | lucht | 880 | 65 |