Hardmetaal(widia): Eigenschappen en toepassingen
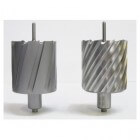
Ontwikkeling van hardmetaal in zes historische stappen
- In de 19e eeuw wordt snijgereedschap gemaakt van koolstofhoudend staal. Het geharde gesmede gereedschap verspaant constructiestaal met snijsnelheden van enkele meters per minuut. De standtijd is kort omdat door warmteontwikkeling van de snijsnede het gereedschap door ontlaten bot wordt.
- Mushet ontdekt in 1868 dat toevoeging van wolfram aan staal, de hardheid verhoogt. En daarmee de snijsnelheid en standtijd, hij produceert de eerste commerciële legering. Het is de bases van de snelle ontwikkeling van verspanings gereedschap.
- Rond 1900 introduceert Taylor het High Speed Steel (HSS), dat gebaseerd is op secundaire harding, het betekent wederom een flinke verhoging van snijsnelheid en standtijd.
- In 1915 de introductie van gietlegeringen op basis van Kobalt, Chroom, Wolfram enz. Deze legeringen bevatten ongeveer 50% harde carbides. Een voorbeeld is Stelliet. Stelliet is hard maar bros en wordt als snijmateriaal op stalen schachten gesoldeerd.
- Hardmetaal ontstaat in de jaren 20 onder de naam “Widia”, (“Wie Diamant”).
- In de jaren 30 wederom een verbetering in de snijmaterialen. Namelijk de gesinterde carbides, met Wolfram-carbide en kobalt als bindende matrix.
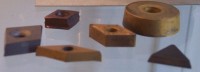
De bases van het sinteren
Sinteren is een warmtebehandeling bij hoge temperatuur, het verhitten en afkoelen geschiedt gecontroleerd. Carbides worden vermaald tot poeder met een bepaalde korrelgrootte. Het carbide poeder wordt in een stalen matrijs in de vorm geperst. Dit halffabrikaat is 50% poreus en in deze toestand prima te bewerken. De carbide korrels worden verhit tot een temperatuur onder hun smeltpunt. De korrels wellen aan elkaar, waardoor een hard materiaal ontstaat. Weinig materialen zijn volgens de hardheidsschaal van Mohs harder dan gesinterd wolframcarbide. Sinteren bepaalt de eindafmeting van het product, de porositeit verdwijnt en dat veroorzaakt een materiaal krimp van circa 20%.Solid state- en liquid phase sintering
Bij solid-state sintering wordt de carbide poeder door een bakproces aaneen geweld zonder dat smelten optreedt.
Bij Liquid-phase sintering wordt op baktemperatuur een gedeelte van het materiaal (de matrix kobalt) vloeibaar. Deze vloeistof zal door capillaire werking de poriën tussen carbide korrels opvullen. Het hardmetaal bestaat dus uit Wolfram-carbide als harde en slijtvaste basis, gebonden met kobalt als matrix, kobalt is hier de enige element die tijdens sinteren smelt. De hardmetalen snijplaatjes worden gesoldeerd of geklemd op een stalen snijplaathouder.
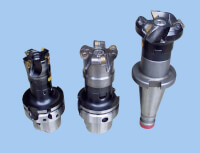
Gecoat gecementeerd hardmetaal
Circa 85% van de snijgereedschap bestaat uit gecoat gecementeerd hardmetaal. Het succes is gevolg van de combinatie van slijtvastheid en taaiheid. Het cementeren is het “versmelten” van de carbides.CVD coating
CVD staat voor Chemical Vapor Deposition (chemische dampafzetting). De CVD coating wordt gegenereerd door chemische reacties bij temperaturen van 700-1050°C. CVD coatings kennen een grotere slijtvastheid en uitstekende hechting aan gecementeerd hardmetaal. De eerste CVD coating op gecementeerd hardmetaal is een enkelvoudige laag titaniumcarbide (TiC). Recent is titaniumkoolstofnitride coating MT-TiCN ontwikkeld. Deze coating verhoogt de abrasieve slijtvastheid, waardoor minder flankslijtage.
PVD (Physical Vapor Deposition) coating
PVD staat voor Physical Vapor Deposition (fysische dampafzetting). De coating wordt gevormd bij (400-600°C). gebaseerd op verdamping van een metaal in een stikstof milieu, waardoor een harde nitride coating neerslaat op het oppervlak van het hardmetaal. De harde PVD coating zorgt wederom voor betere slijtvastheid. De componenten van de PVD-coating staan hieronder vermeld, moderne coatings zijn combinaties van deze componenten, in opeenvolgende lagen aangebracht.
PVD coating | Belangrijkste eigenschappen |
---|---|
PVD-TiN | Titanium-nitride. De goudkleurige coating heeft all-round eigenschappen |
PVD-TiCN | Titanium-koolstof-nitride is harder dan TiN en voegt dus slijtagebestendigheid toe |
PVD-TiAlN | Titanium-aluminium-nitride verhoogt hardheid en oxidatieweerstand |
PVD-oxide | Wordt gebruikt omdat het chemisch inert is en een betere krater slijtvastheid. |
Carbiden
Smelttemperatuur °C | Carbide verbindingen |
---|---|
3875-3700 | HfC, TaC |
3700-3300 | NbC, ZrC |
3500-3050 | HfB2, ZrB2, TaB2, TiC, HfN, Th02 |
3050 - 2750 | TiB2' VC, TaN, ZrN, TiN, Hf02', Zr02, WC |
2750 - 2500 | Al4C3, M02C, BeO, Ca0 |
2500 - 2300 | LaB6, B4C, SiC, AlN, VN, Cr203 |
2300 - 1950 | Aluminiumoxide (Al203) |
De in hardmetaal gebruikte carbiden hebben een hardheid van circa 9 op de schaal van Mohs. De hardheid van de "lijmende" matrix kobalt is 5 op die schaal, smeltpuntvan kobalt is 1495 °C en kookpunt 2900 °C. Verweking en smelten van de matrix kobalt ligt dus beduidend lager als van de carbiden.
Korrelgrootte carbides
Korrelgrootte van de carbides is mede bepalend voor de hardheid/taaiheid relatie van het hardmetaal. Hoe fijner de korrel, des te hoger de hardheid. De hoeveelheid van de Kobalt lijmende matrix bepaalt de taaiheid van het hardmetaal en daarmee de weerstand tegen plastische vervorming. Te weinig bindende matrix leidt tot brosheid.
Hardheidsschaal van Mohs
We vergelijken de hardheid van stoffen door de ene stof met de andere te krassen. Daarop is de hardheidschaal van Mohs gebaseerd. Het mineraal met hardheid 1 is het zachtst en het mineraal met hardheid 10 het hardst. Half edelstenen hebben een hardheid van 7. Mineralen met een hardheid hoger dan 7 zijn edelstenen. Eigenlijk moet men hier hiet spreken van hardheid maar van krasweerstand.Hardheid | Omschrijving van de hardheid |
---|---|
1 | Een steen met hardheid 1 maakt op papier een streep |
2 | De vingernagel maakt een kras op een steen met hardheid 2-2,5 |
3 | Een koperen munt maakt een kras op een steen tot hardheid 3-3,5 |
4 en 5 | Glas maakt een kras in steen tot hardheid 5-5,5 |
6 | Een stalen kraspen krast met veel druk op glas |
7 | Kwarts met een hardheid van 7 krast glas en staal |
8 | Topaas krast kwarts |
9 | Korund krast Topaas |
10 | Diamant (de hardste natuurlijke stof) |
Indeling van hardmetaal in drie groepen
Hardmetaal groep | Specificatie |
---|---|
WC-Co | Kobaltgebonden wolfraamcarbiden |
W,X-Co | waarin X=Ti,Nb,V.Ta |
TiC-(Mo-Ni) | --- |
Gecoate hardmetalen snijplaatjes
Opdampen gecombineerd met een chemische reactie (900 °C). Door het TiC-laagje is een reductie van ongeveer 20% in snijkracht en een verlaging van de verspaningstemperatuur van circa 150 °C het gevolg. Dit leidt tot verdubbeling van de snijsnelheid bij dezelfde standtijd.Materiaal | Uitzettingscoefficient |
---|---|
WC-Co | 5-7.10-6 |
TiC | 7,42x10-6 |
TiN | 9,35x10-6 |
Titaankarbide/ titaannitride - coating
Op het oppervlak kan een laagje zuiver titaancarbide TiC aangebracht worden. Ook titaannitride TiN wordt als coating aangebracht. Aangezien TiN mengbaar is met TiC is het mogelijk om lagen met overgangsgebieden op te dampen. Men verkrijgt hierdoor een meer geleidelijke overgang van TiC naar TiN, hetgeen van belang is in verband met het verschil in uitzettingscoëfficiënt van beide lagen, zoals in voorgaande tabel is te lezen