High strength low alloy (HSLA) staalsoorten
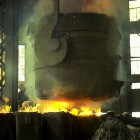
HSLA (High-strength low-alloy) staal
HSLA staal heeft betere mechanische eigenschappen, betere lasbaarheid en een grotere weerbestendigheid dan koolstofstaal. Nadruk ligt bij deze staalsoort op de toepassing, niet op een in normbladen vastgelegde chemische samenstelling. Om de gewenste eigenschappen te realiseren wordt bij het walsen van dunne plaat van een andere chemische samenstelling uitgegaan dan bij het walsen van dikke platen. Bij de HSLA staalbereiding belangrijke afkoelkarakteristiek is immers afhankelijk van de staalmassa.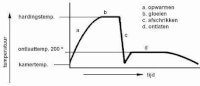
[OLIST]Staal met laag koolstofgehalte wordt gelegeerd met circa 1 % mangaan en gecontroleerd gewalst en afgekoeld. Het mangaan vertraagt de transformatie van austeniet naar ferriet zodat door “onderkoeling” een fijne ferriet/perliet korrel wordt gevormd. Door het afwalsen wordt tevens de ferrietische matrix structuur verstevigd door deformatie. Beide korrelverfijning en versteviging leiden tot hogere sterkte.
Staal met een laag koolstofgehalte van 0,08-0,25%, om de lasbaarheid te garanderen, wordt microgelegeerd met carbide vormende elementen als, chroom, vanadium, niobium, titanium, zirkonium. Door het gecontroleerd walsen en afkoelen treedt precipitatie harden op. Het eindresultaat is een lasbaar staal met hoge sterkte en redelijke taaiheid vanwege de taaie ferritisch/perlitische matrix.[/OLIST]
Conventioneel staal
Normaal laaggelegeerd staal vereist een kostbare aparte warmtebehandeling om aan de gewenste mechanische eigenschappen te komen: verhitten in austenietgebied, afschrikken tot een martensiet structuur en deze laag ontlaten (circa 200°C) met nadruk op sterkte of hoog ontlaten (circa 550 °C) met nadruk op veredelen, d.w.z. een compromis tussen sterkte en taaiheid.Microstructuren van een HSLA staal met - 0.13C, 1.3Mn
HSLA staal kan in beginsel bestaan uit een ferritische-ferritische/perlitische-, bainitische-, of martensitische matrix. De strekgrens van HSLA staal varieert daardoor van 260 N/mm2 tot meer dan 1000 N/mm2. De matrix van de microlegering scheidt carbides en nitrides uit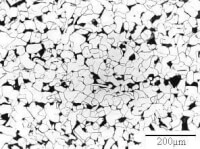
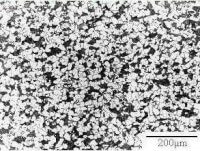
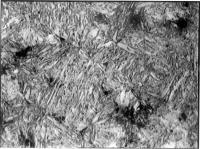
Indeling HSLA stalen op bases van belangrijkste kenmerken
- Weervaststaal door toevoeging van kleine hoeveelheid Koper, silicium, nikkel, chroom en fosfor om een beschermende oxidelaag te vormen op het oppervlak. En tevens een bijdrage te leveren aan de sterkte en taaiheid.
- Microalloyed ferrite-perlite staal, bevat zeer kleine (minder dan 0.10%) toevoegingen van carbide of nitride vormende elementen zoals niobium, vanadium, titanium. Ze zijn nodig voor precipitatie harding, korrelverfijning en beïnvloeding van de transformatie temperatuur van austeniet naar ferriet.
- Gewalst perlitisch staal, waaronder koolstof-mangaan staal bevat tevens een kleine hoeveelheid andere legeringselementen om de gewenste mechanische eigenschappen te bereiken.
- Laag gekoold bainiet staal met minder dan 0,05% C, een prima combinatie van strekgrens, (tot circa 690 N/mm2) taaiheid en lasbaarheid.
- DP staal (Dual-phase staal), heeft microstructuur van harde martensiet verspreid in een taaie ferriet matrix, een combinatie van taaiheid en hoge treksterkte.
- Gecontroleerde insluitselvorm, verbeterde vervormbaarheid en taaiheid door toevoegingen van slechts weinig calcium, zirkonium, titaan en soms zeldzame aarden die de vorm van sulfideninsluitsels verandert van scherpe lamellen in bolvormig korrels.
Invloed van micro-legeringselementen
Vanadium en NiobiumToevoeging van kleine hoeveelheid (<0,10% elk) Niobium en vanadium verhoogt de sterkte van koolstofstaal, zonder andere eigenschappen te ontregelen. We kunnen het koolstofgehalte verminderen, waardoor de lasbaarheid en taaiheid verbeteren, de precipitatieharding door Niobium- en vanadiumcarbiden compenseert de sterkte vermindering door de koolstof afname.
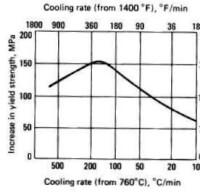
Figuur 5 geeft het effect weer van de afkoelsnelheid op de strekgrensverhoging door precipitatie harding in 0.15% koolstof staal met vanadium. Bij een afkoelsnelheid van 175 °C per seconde wordt maximum stijging van de strekgrens van 150 N/mm2 bereikt. Vanadium (max. 0.10%) verhoogt de sterkte door vorming van fijne precipitaten vanadium-carbide-nitride V(CN) in ferriet, tijdens afkoelen na warmwalsen. Vanadium precipitaten zijn opgelost in austeniet bij walstemperatuur en hebben bij afkoeling tijd nodig om te diffunderen en carbides te vormen. Is de afkoelsnelheid te groot dan is die tijd niet beschikbaar en blijft vanadium in geforceerde oplossing. De afkoelsnelheid, mede bepaald door plaatdikte, bepaalt de mate van precipitatieharding (zie figuur 5). De V(CN) precipitaten zijn minder effectief bij het versterken bij hogere afkoelsnelheid, er blijven meer elementen in oplossing en minder vanadium-carbiden-nitriden precipiteren door tijdgebrek.
Mangaan
Mangaan heeft invloed op de versterking van voorgenoemde vanadium- microgelegeerd staal. Bij 1% toename van het mangaangehalte verhoogt de sterkte (van de matrix) met circa 37 N/mm2. Bovendien wordt de versterking door vanadium extra vergroot omdat mangaan de austeniet- ferriet transformatietemperatuur verlaagd, wat resulteert in een fijnere uitscheiding (dispersie)van de carbides/nitriden.
Invloed mangaan op vanadium (microgelegeerd) staal met 0,08%C en 0,30%Si silicium
Staal met 0,3% Mangaan
- 0,00% V: strekgrens 297 N/mm2
- 0,08% V: strekgrens 352 N/mm2
- 0,14% V: strekgrens 380 N/mm2
Staal met 1,2% Mangaan
- 0,00% V: strekgrens 331 N/mm2
- 0,08% V: strekgrens 462 N/mm2
- 0,14% V: strekgrens 552 N/mm2
Niobium
Niobium en titanium zijn tevens korrelverfijners. Zoals vanadium, verhoogt ook niobium de vloeigrens door precipitatie harden, en hangt de grootte van de verhoging af van de hoeveelheid gevormde niobiumcarbiden. Niobium is een doeltreffender korrelverfijner dan vanadium, het combineert de uitscheiding (precipitatie) versterking met een fijnere ferriet korrel die eveneens tot versterking leidt, niobium is daarom een doeltreffender versterkingselement dan vanadium.
Sulfide insluitsels
Zirkonium en calcium worden toegevoegd om sulfide-insluitsel bolvormig te maken, nodig omdat de HSLA staalsoorten anisotroop zijn dwz de mechanische eigenschappen afhankelijk zijn van de richting van de belasting t.o.v. de walsrichting.
Molybdeen in HSLA constructiestaal
Blauw 1: MoNbV snel afkoelen °C/sec.
Geel 1: MoNbV langzaam afkoelen aan de lucht.
Blauw 2: MoNb snelafkoelen °C/sec.
Geel 2: MoNb langzaam afkoelen aan de lucht.
Mo wordt toegevoegd aan HSLA staal wanneer de vloeigrens a) boven 550 N/mm2 moet komen, of b) er wordt een bepaalde microstructuur gevraagd. Mo is vooral gunstig voor de vorming van bainiet. Titanium, vanadium, Niobium worden toegevoegd voor versterking. Deze elementen zijn bedoeld om een fijne dispersie van carbides te produceren om de microstructuur, ferriet-perliet, in een bijna ferriet matrix te veranderen door onttrekken van koolstof aan het perliet. Dit vergroot de taaiheid van de matrix, en vergroot de sterkte door een fijnere korrel. In geval van een ferrietmatrix neemt de sterkte toe met 50%, bij halvering van de korrelgrote. Bij brand bezwijkt de strekgrens door het z.g.n kruipen van het staal van het dragende staalskelet en de constructie bezwijkt onder eigen gewicht. Daarom moet brandbestendig staal bij temperaturen van 400-700 ° C gedurende enkele uren het kruipen vertragen. HSLA staal met toevoegingen van Nb, Mo, V en/of Ti vertonen beduidend grotere weerstand tegen kruipen in vergelijking met gewone koolstofstaal. Mo gelegeerde staal presteert het best. Mo versterkt het staal door verharding van ferriet en door precipitatie van Molybdeencarbide die als ankers fungeren.
Korrelgrote
De sterkte van staal, dus ook van vanadiumstaal, wordt mede bepaald door de korrelgrote van het ferriet, dat ontstaat tijdens afkoeling vanaf de austeniet gebied. Fijnere ferriet korrels (waardoor hogere sterke, maar ook verbeterde vervormbaarheid) wordt gerealiseerd door lager austeniet- ferriet transformatie temperatuur of door de vorming van fijnere austeniet korrel vóór de transformatie. Verlaging van de transformatietemperatuur kan worden bereikt door legeren met genoemde elementen en /of hogere afkoelsnelheid waardoor door de druk van de onderkoeling kleinere korrels gevormd worden.Methoden om een fijnere korrel te creëren
[OLIST]Normaalgloeien na warmwalsen.
Afwalsen laag in het tweefasen gebied austeniet/ferriet (normaliserend walsen).
Toevoegen van V, Nb, Ti en Al in combinatie met N (microgelegeerd=HSLA staal).
Combinatie van 2 en 3 (TMCP=Thermo Mechanical Controlled Processing (TM-staal).
Afgeschrikt en getemperd staal met toevoeging van Cr, Mo, Ni, Cu voor doorharding.[/OLIST]
De relatie korrelgrote- strekgrens
Volgens de Hall-Petch-relatie neemt de strekgrens van staal toe met afnemende korrelgrootte volgens:
- σR = σO + k √(1/d); waarin d de gemiddelde korrelgrote.
- σR is de strekgrens N/mm2.
- σO is de oorspronkelijke strekgrens voor de verandering van de korrelgrote.
- d is de gemiddelde diameter van de korrels.
- K is een materiaalconstante.
Rekristallisatie
Tijdens het warmwalsen van staal in het austeniet gebied zal door de aangebrachte deformatie rekristallisatie en daardoor korrelverfijning optreden. Ligt de warmwalstemperatuur boven de rekristallisatie temperatuur van het staal treedt bij die hoge temperaturen korrelgroei op. Staalproducenten beheersen met de moderne meet en regeltechniek de korrelgrote tijdens het warmwalsen.
Austempering
Austempering wordt gedaan om taaiheid te realiseren in een werkstuk met gecompliceerde vorm, als er teveel risico is dat afschrikscheuren ontstaan bij conventioneel afschrikken en ontlaten. De afkoelspanning tijdens austempering zijn veel lager omdat de koeling van 840°C tot 300°C geen faseveranderingen inhoudt en omdat de trage isotherme transformatie van austeniet naar bainiet overal in het product praktisch gelijktijdig plaats vindt en er geen temperatuurgradient is.Thermomechanisch walsen
Ligt de walstemperatuur boven de rekristallisatietemperatuur van het staal treedt korrelgroei op. Deze korrelgroei wordt voorkomen door toevoeging van een kleine hoeveelheid legeringselementen zoals vanadium, Niobium, titaan. Ze vormen carbides die zich vestigen aan de korrelgrenzen en in de korrels zelf. Deze deeltjes beperken de korrelgroei, ze verankeren de korrels tijdens het warmwalsen. Door gecontroleerd walsen krijgt het staal geen tijd om te rekristalliseren dat gebeurt aan het einde van het walsproces bij lage temperatuur, waardoor een fijne korrel ontstaat. De meeste staalfabrikanten kiezen voor een afwalstemperatuur onder in het austenietgebied, maar het afwalsen mag ook in het lagere austeniet-ferrietgebied liggen. Afwalsen in het austeniet-ferrietgebied leidt tot een extra sterkte, hoe lager de afwals temperatuur hoe hoger de sterkte.Afschrikken en temperen
De QT staalsoorten zijn speciaal ontwikkeld voor gelaste constructies. De strekgrens van deze materialen varieert van 350 N/mm2 tot 1050 N/mm2 afhankelijk van de chemische samenstelling, plaatdikte en warmtebehandeling. Na afschrikken moet een martensietstructuur ontstaan. Ontlaat temperatuur tussen 540 °C en 650 °C, geeft een structuur van ontlaten martensiet en lager bainiet. Om goed lasbaar te zijn, mag het koolstofgehalte van deze materialen niet hoger zijn dan 0,2%. Om na het lassen de vorming van perliet, ferriet en hoog bainiet te voorkomen moet de afkoelsnelheid voldoende groot zijn om martensiet en laag bainiet te vormen. Omdat de vorming van martensiet al op een temperatuur van circa 400 °C start, zal als gevolg van de relatief langzame afkoeling van de lasconstructie een zelfontlaateffect optreden. Het gevolg is een lasverbinding met een goede taaiheid, waardoor geen warmtebehandeling na het lassen nodig is. Een geïntegreerde warmtebehandeling in het walsproces.HSLA Legering A633; Chemische samenstelling in%
grade | A % | C % | D % | E % | staalplaatdikte |
---|---|---|---|---|---|
koolstof | 0,18 max | 0,20 max | 0,20 max | 0,22 max | --- |
mangaan | 1,0-1,35 | 1,15-1,5 | 0,7-1,35 | 1,15-1,5 | < 38mm |
mangaan | 1,0-1,35 | 1,15-1,5 | 1,0-1,60 | 1,15-1,5 | 38-100mm |
mangaan | ---. | --- | --- | 1,15-1,5 | 100-150 mm |
fosfor | 0,35 max | 0,35 max | 0,35 max | 0,35 max | --- |
zwavel | 0,40 max | 0,40 max | 0,40 max | 0,40 max | --- |
silicium | 0,15-0,50 | 0,15-0,50 | 0,15-0,50 | 0,15-0,50 | --- |
vanadium | --- | --- | --- | 0,04-0,10 | --- |
niobium | 0,05 max | 0,01-0,05 | --- | --- | --- |
nitrogen | --- | --- | --- | 0,03 max | --- |
koper | --- | --- | 0,35 max | --- | --- |
nikkel | --- | --- | 0,25 max | --- | --- |
chroom | --- | --- | 0,25 max | --- | --- |
molybdeen | --- | --- | --- | 0,08 max | --- |
A656 HSLA Staal grades 50, 60, 70, 80
656 HSLA staal omvat drie types(3, 7 en 8) en vier sterktes (50, 60, 70 en 80), stalen plaat voor vrachtwagen, kranen, treinstellen, e.d. worden meestal geleverd in gewalste toestand.Legering A656; Chemische samenstelling
grade → | type 3 | type 7 | type 8 |
---|---|---|---|
koolstof | 0,18 max | 0,18 max | 0,18 max |
mangaan | 1,65 max | 1,65 max | 1,65 max |
fosfor | 0,025 max | 0,025 max | 0,025 max |
zwavel | 0,035 max | 0,035 max | 0,035 max |
silicium | 0,60 max | 0,60 max | 0,60 max |
vanadium | 0,08 max | 0,15 max | 0,15 max |
nitrogen | 0,020 max | 0,020 max | 0,020 max |
niobium | 0,08 - 0,10 | 0,10 max | 0,10 max |
titanium | --- | --- | 0,15 max |
Cor-ten weervaststaal
Weersvaste stalen zijn ASTM: A588, A242, A606-4, A847, A709. Het oorspronkelijke weervaste staal waar de ontwikkeling van de HSLA stalen mee begon is Cor-ten staal. Het roestvertragende effect van de oxidelaag wordt veroorzaakt door legering elementen. Het weervaste Cortenstaal wordt gebruikt zonder verf voor bijvoorbeeld bruggen. Voordeel van het staal bij buitengebruik is dat er relatief weinig onderhoud is ideaal voor bruggen en constructies waar de werkplek voor onderhoud gevaarlijk is.Richtwaarden mechanische eigenschappen van bekende HSLA stalen
HSLA staal | strekgrens min N/mm2 | breukrek % min | plaatdikte mm max |
---|---|---|---|
A709 Gr36 | 250 | 21 | --- |
A709 Gr50 | 345 | 19 | --- |
A572 Gr42 | [/TD][TD] | [/TD] | |
345 | 21 | [/TD] | |
[/TD][TD] | [/TD] | ||
345 | 19 | 19 | |
weerbestendig A588(cor-ten B) | 345 | 19 | 100 |
656 Gr50 | 345 | 23 | 50 |
656 Gr60 | 415 | 20 | 38 |
656 Gr70 | 480 | 17 | 25 |
A656 Gr80 | 550 | 15 | 19 |
koudebestendig tot -45oC A633 GrA | 290 | 18 | 100 |
koudebestendig tot -45oC A633 Gr C/D | 340 | 18 | 65 |
idem | 310 | 18 | 65- 100 |
koudebestendig tot -45oC A633 GrE | 410 | 18 | 100 |
idem | 380 | 18 | 100-150 |
Staalsoort | C | Si | Mn | P | S | andere |
---|---|---|---|---|---|---|
A572 | 0,21-0,26 | 0,15-0,40 | 1,35-1,65 | max0,04 | max 0,05 | --- |
Bewerkbaarheid HSLA staal
Verpanende bewerking:HSLA staal is goed te verspanen
Kouddeformatie:
Vooral het Dual Phase staal (DP staal) is goed koud te vervormen en wordt als dieptrekstaal beschouwd.
Lasbaarheid en koolstofequivalent
Het staal is goed te lassen door het lage koolstof percentage. Een maat voor de lasbaarheid is het koolstofequivalent Ceq dat met de volgende formule geschat kan worden: Ceq = C + Mn/6 + (Cr + Mo + V)/5 + (Ni + Cu)/15
Voor een goede lasbaarheid van constructiestaal tot 40 mm dikte en minimale strekgrens van 235 N/mm2 moet volgens NEN-EN 10025 de koolstofequivalent lager zijn dan 0,35.
Een belangrijk voordeel is dat deze HSLA staalsoorten door de lage koolstofgehalte meestal zonder voorwarmen gelast kunnen worden, ze zijn minder gevoelig voor koudscheuren. In de warmtebeïnvloede zone (WBZ) hebben ze een hogere kerfslagwaarde dan normaal gegloeid staal. Het is mede gevolg van de korrelgroei remmende carbide vormende elementen in de laszone. HSLA-staalsoorten worden om die reden toegepast in zwaar belaste lasconstructies.
Toepassing
De HSLA constructiestalen worden gebruikt in constructies die staal met een goede sterkte-gewicht verhouding nodig hebben. HSLA staalsoorten zijn gemiddeld circa 25% lichter dan een koolstofstaal in dezelfde toepassing.- Staalconstructiein de bouw: strekgrens 460 N/mm2
- Gastransportleidingen,drukvaten:strekgrens: 480 N/mm2
- Beweegbare bruggen, kranen vrachtwagens achtbanen: strekgrens 690 N/mm2
- Onderzeeboten: strekgrens 1100 N/mm2